
Workplace Safety: Your #1 Defense Against Workers’ Compensation Costs
Whether you’re a small business owner or the CEO of a national operation, part of running your business smoothly is keeping your employees safe. Part of accomplishing this is having a workers’ compensation policy in place to provide injured workers with medical care and compensation for a portion of the income they lose while they are unable to return to work, as well as protecting your organization from lawsuits by workers injured while working.
Workers Compensation costs can be significant depending on the severity of the injury to your employee. This is why having coverage in place is extremely important in industries where employees are at a daily risk for injury. According to the Insurance Journal, in 2012 alone, overexertion cost over $15 billion dollars and accounted for 25.3% of workplace injury costs! So, what is the best way to avoid injury in the workplace and drive the cost of workers’ compensation down in your organization? Workplace safety.
Safety is the #1 way to reduce your workers’ compensation costs. Not only can safety measures directly affect your insurance premium, they can also affect indirect costs such as hiring, retraining, overtime, loss of productivity and more. Research shows that for every $1 invested in workplace safety, employers realize $3 - $10 in cost savings. If you make workplace safety a top priority now, you’ll see the impact in the future. Below are some tips to creating an effective safety program for your organization.
Creating a Workplace Safety Program
Identify Hazards and Assess Risks
Every organization has unique hazards and risks, so it is important to take the time to identify them. A hazard is an event or situation that has the potential to cause harm, such as clutter blocking fire exits, aisles and emergency exits. A risk is the likelihood of someone being harmed by that hazard along with how severe the harm could be. You are not obligated by law to eliminate every risk, but you are required to protect your employees as far as reasonably practical.
Start by inspecting your workplace for any identifiable hazards. Here are three types of hazards to be aware of:
- Workplace Hazards, such as a workshop’s layout.
- Activity Hazards, such as lifting heavy objects for an extended period of time.
- Environmental Hazards, such as the sawdust that accumulated from wood cutting.
After you have done your walkthrough, do not hesitate to ask your employees if they have noticed any additional hazards that may not be immediately obvious to you. After all, they are the ones who would be exposed to various risks.
Yourself and your management team should clearly lay out the safety requirements employees must follow. The ideal place to include these requirements is in writing within employee job descriptions. Here you can state specifically the requirements and issues regarding health and safety responsibilities pertaining to a specific position. It is vital to have this in writing so there is less opportunity for misinterpretation and uncertainty. Not every safety regulation requires written plans. According to OSHA, there are several safety regulations that actually do require a written plan:
- Hazard Communication Program.
- Lockout / Tagout Program (energy control procedures).
- Respiratory Protection Program.
- Personal Protective Equipment (hazard assessment).
- Bloodborne Pathogens Post-exposure Plan.
- Emergency Actions Plans.
- Permit-required Confined Spaces.
- Electrical Safety.
- Fire Prevention Plan.
- Hearing Conservation Program.
- Trenching and Excavation Safety.
Educate Employees
Truly instilling your organizations safety philosophy into your employees is one of the most crucial aspects of creating and maintaining an effective Workplace Safety Program. To do this will take time, but it will result in less injury and illness throughout your organization. Studies indicate that employees who are new on the job have a higher rate of injuries and accidents compared to more experienced workers. This should be a huge motivation for your organization to implement a training program as a solution.
There are numerous OSHA standards that specifically require the employer to train employees in the health and safety aspects of their unique position. Here are some voluntary OSHA training guidelines to assist you in providing the safety and health information and instruction needed for your employees to work at minimal risk to themselves, to fellow employees and to the public.
The best times to provide training are when you first hire an employee, transfer an employee to a new department or give them new responsibilities, change or implement new processes, uncover special hazards or risks that were not previously identified, and when offering a refresher.
Report/Investigate all Accidents and Incidents
No matter the severity of an incident, it should always be reported and investigated. Although you cannot control the outcome of an incident that has already happened, you can gain knowledge from it in efforts to prevent the same incident in the future. Your investigation should include these items:
- What caused the incident? Ask the injured employee(s) and witness(s) for information on the incident being careful not to place blame; you are on a mission to get the facts that will stop this from happening again in the future.
- How can you reduce this risk?
- Take action and monitor results. Create a safety measure to address this risk and pay attention to if this new measure has decreased this type of incident.
Evaluate Safety Processes Annually
Set up a time every year to review your safety procedures and identify the strengths and weaknesses within them. Use this to improve your procedures and ultimately reduce accidents and injuries in the workplace. Activate new and alter existing procedures as needed.
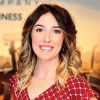